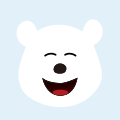
E-Gas 知识梳理
“ 学习E-Gas 6.0 版本,域控,电机,项目功能安全设计参考”
参考文件 6.0
专业术语
- driving cycle
在传统车的角度指的是发动机启动/停止之间的操作时间,对于纯电动来说由BMS指定。作为域控可以通过报文来解析获取该信息。
- error or a single error
在需要考虑的特性里面至少有一个不能完全满足则可以定义为 error or a single error
- error
如果在下一个driving cycle没有发生,并且驾驶员或者是控制器也没有检测到相关故障,则这个error需要被定义为 潜在的error
- double error
需要定义为两个error,都发生几乎在同一时刻发生,并且这两个故障没有因果关系
- dual error
需要定义为两个single error,都发生(时间间隔超过一个很短的时间),并且这两个故障没有因果关系
- fault detection
当相关系统参数的超过允许偏差,导致不满足至少一个有关所考虑单元的要求特性的要求。这里设定一个检测时间。来减少误判,如果在这一事件内被检测到 则定义为已检测到错误。
- failure effect
需要在无故障下和有故障下根据系统的具体特性偏差来指定。
- failure reaction
在发生故障后,开始一套完整的手段,响应,来减少故障带来的影响,将破坏降低到一个被允许的限度。
- Controllable failure reactions
○ 响应时间
○ 整车行为限制,扭矩,转速,加速度等
- Raw signals
○ 硬件寄存器采样的数字信号或者模拟信号
○ 总线当前的没有被更改过的数据
- Reset
○ SW reset 被软件控制的初始化 判断影响范围 (ram, rom, etc)
○ HW reset 被硬件初始化 判断影响范围(看门狗,上下点,等等)
开发指导基本准则
- 优先考虑保护生命,声明作为最重要的考虑点。
- 能用可靠性解决的不要使用退而求其次的备用方案。可靠性优先于备份功能。
- 检测机制应该独立于功能,并且尽可能的独立于驾驶员的反应。
- 系统监控包括故障响应,需要简单的,并且可控便于管理的。
- 系统设计应当使single error, error 发生或者同时发生时系统反应时可控的。监控的相关信号路径应该是从传感器,到执行机构,到功能层面都要被监控
- 就高系统可用性来说,应争取阶段性错误反应。
- ”confirmed defected", "explicit detection", "assumed defected",当一个故障在被检测到后,过了系统定义的次数或者时间后变成了"explicit detection"。在reaction执行之前都被认为 "assumed defected"。
- 适当的reaction需要设计,当系统处于 "assumed defected"阶段。当然在”confirmed defected"这时候reaction是必须的。
- reset这种故障响应,需要视情况而定,必须是可控的情况下。避免很多不连续的情况发生或者导致系统不连续的情况发生。
- 当系统不受控制,或者达不到可控的范围,这时候可以请求停机。这里的停机指的是将车辆请求到一个功能安全定义的安全感状态。
- 信号传输,发送方需要保证信号的有效真实完整性
- 当error发生,或者一系列的errors发生,系统出现了不可预测的响应,这时候需要提醒驾驶员。必要的时候改变驾驶形式。
- 监控功能需要有较高的鲁棒性,简单性
- 在每一次driving cycle钱需要进行关断路径测试,检测其有效性。和科目三驾驶员绕车转一圈一个意思。
- 当检测到电源有问题后,关断路径的检测依然应该是可用的。需要对电源进行监控,避免损坏其他部件。
- 安全理念需要遵循ISO26262
系统定义
概念从下图简单系统定义进行说起
功能安全设计的最开始需要定义清楚每个部件的边界,以及系统边界图。
有了完整的系统边界图,才对下面的安全分析有方向性,和目标性。
Hazard 和 Risk 分析
作为Hazard 和Risk 分析的一部分,分析了典型驾驶情况下系统的行为。基于上面的系统做了个简单的分析定义。并得出一下结果。这是从最顶层的分析结果。
Safety Goal
- SZ-01 Prevention of unintended acceleration → ASIL B
- SZ-02 Prevention absence of acceleration → QM
- SZ-03 Prevention of unintended deceleration → QM
- SZ-04 Prevention absence of deceleration → QM
从上面分析,无意识加速时需要考虑的。需要被监控的。并且需要定义一个fault tolerance time(fft)
下面的概念,以及设计都是为了达到SZ-01这个 GOAL 来实施的。
功能安全概念
分析哪些部件可能导致车子无意识加速
- 错误的扭矩
扭矩来自于哪里发动机,电机,扭矩监控出问题,执行件出了问题。
所以要对下面的component 进行一下安全要求(safety requirement)
- sensor
在捕获信号后,可对传感器信号(例如驾驶员加速踏板需求)进行合理性检查。
- actuators
执行器(A)在捕获执行器信号后,可以对执行器信号(例如油门位置)进行合理性检查
- Engine control unit
○ 可以检测并确认不允许的高驱动扭矩设置
○ 并将系统作为故障反应带入安全状态
○ 安全概念采用了中央功能监控(2级)的理念。
○ 发动机控制单元检测传感器系统故障。
○ 发动机控制单元检测执行器故障。
○ 在发动机控制单元中实现了安全概念
Central 功能监控:
- 无论功能级别(1级)如何,被监控的功能都应在功能监控级别(2级)中进行计算,并在发生错误时将其控制在可控范围内。
- 独立开发确保系统错误不会对功能层(第1层)和监控层(第2层)产生相同的影响。应在控制单元中实施附加措施,以验证所应用ECU硬件的完整性。
- 应确保位于1级和ECU-HW中的错误不会对2级产生未被发现的影响。
技术实施
监控概念
System Overview Electronic Control Unit (ECU)
- level1
- 功能层。
- 一级包含发动机控制功能,即实现所要求的发动机扭矩,组件监控,输入、输出变量诊断和控制系统反应应检测到故障
- level2
- 功能监控级别
- 第2级检测第1级功能软件的缺陷过程,例如通过监控计算扭矩值或车辆加速度。当发生故障时,触发系统反应。
- level3
- 控制器监控级别
- 监控模块应是功能控制器,它在问答交互过程中测试正确执行的程序
- 下面是最经典的三层架构图
当然在新版的图里面更新了锁步核的使用。如下图LC
ECU Level 1层的功能
这里需要梳理清楚ECU 包含了哪些Level 1的功能,这里简化一下,简单列几个
需要包括
- 所有的Level 1 层的功能
- 对监控从相关诊断的输入,输出定义
sensor components
- 加速踏板传感器
...
Actuator components
- 油门阀
...
ECU system component
- 扭矩请求单元
...
硬件特性以及诊断需求
这里需要列出上面需要被监控的components 的
- 特性
- 诊断的points
- 检测的方式
- 故障的描述等等
general requirement of level2 function monitoring
- 监控L1层功能
- 对于具有扭矩监测的系统,第2级的中心部分应是单独计算的“允许发动机扭矩”和“实际发动机扭矩”之间的比较。
- 2级加速监控系统的中心部分应该是单独计算的“允许车辆加速度”和“实际车辆加速度”之间的比较。
- 监测第1级故障反应,如果L2不能单独产生故障反应。
- 拥有周期性监控的内存区域计算程序流控制
举个Level 2层监控加速度的例子。
基本原理就是实际的和可能的/合理的/设计的计算进行对比。就得出了L2层的结果。
其他的一些monitor 也是使用类似的机制。这里不进行一一截图。截一张官方给的具体示例图监控加速度。
这一整套需要从最初开始的传感器,一直到实际的车速扭矩等信息的采集。整条链路需要从最上层车的级别去分析,然后深入到最终实现车运动这个动作的部件的角度来分析。
就比如从最上端的理论支撑,哪些部件涉及到。
直到最下面执行“动作”的部件如果运作。都是需要考虑。
下图为驾驶员的动作到功能层以及监控的传递。
Level 3 Controller Monitoring
- 控制器监控是指软件和硬件结构之间的相互作用。
- 它可以检测功能控制器(控制器核心,RAM/ROM中受影响的区域)的故障操作。
- 必要的检查可以作为软件功能(例如存储器测试值和补码)或控制器内部错误检测硬件或两者的组合来执行。
- 只有在以下情况下才允许由控制器内部错误检测硬件进行检查
- 控制器内部错误检测硬件在当前周期内的工作能力
- 应通过对潜在缺陷的测试来验证(例如,在关机路径上渗透ECC)。只有在完成此试验后,才允许发动机启动。
- 控制器内部错误检测硬件的配置是周期性测试的(例如激活ECC)。
一般有一下方面
ROM检测
检测QA机制
- 程序流监控
- 指令集测试
- 功能指令集
- 原子指令集
- 控制器内部故障
采样的检测
- AD转换 等等
reset 系统特性
下图为综合L1,L2,L3 直至整车reaction的路径图。每一个步骤都需要下一层的保障。
可以说L3层更多的是机制本身的实现与确保。对板本身的监控与测试。
系统错误响应
故障反应应考虑以下原则
- 必要的合理性取决于OEM的具体项目要求
- 从故障检测到系统反应开始的最大持续时间应定义为特定故障。(例如扭矩监测基准= 500ms)等等
希望对大家有一点点帮助。谢谢大家阅读
文章转载自公众号:汽车与基础软件
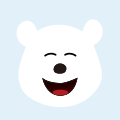